10 Essential Factors to Consider When Choosing a Fastener
Fasteners are critical components that hold together everything from buildings and automobiles to electronics and machinery. While they may seem small, choosing the right fastener is crucial for safety, longevity, and performance. Incorrect selections can lead to structural failure, increased downtime, and additional maintenance costs. This guide outlines the top 10 factors to consider when selecting fasteners to ensure your project is built to last.
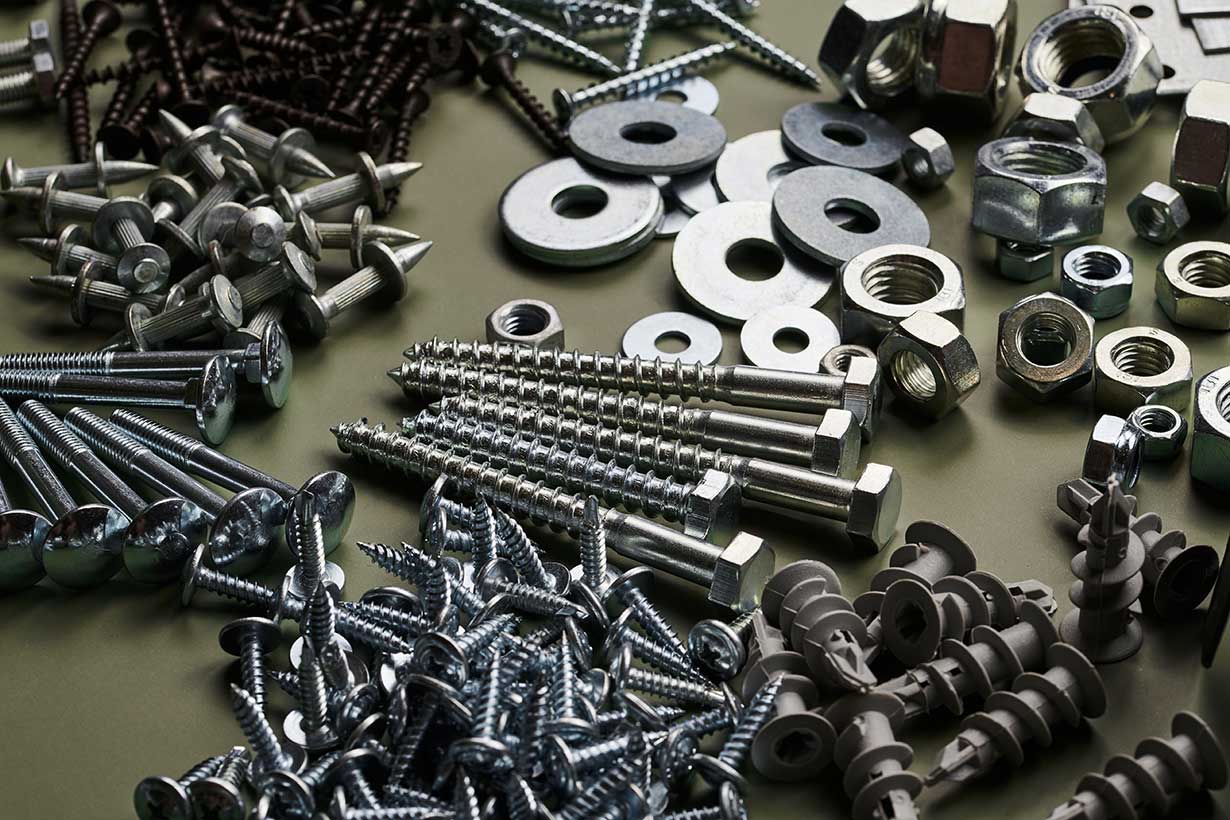
1. Purpose and Functionality
The first factor to consider is the purpose of the fastener. Is it designed for a permanent joint, or will it need to be adjusted frequently? Fasteners like bolts and screws offer flexibility, while rivets provide more permanent connections. For parts that experience high loads or vibration, heavy-duty fasteners that can withstand wear over time may be required.
2. Environmental Conditions
Environmental conditions are crucial. Factors like humidity, temperature, chemical exposure, and UV radiation can affect fastener durability. For outdoor applications or harsh environments, choose corrosion-resistant materials like stainless steel. Lighter materials such as plastic or aluminum may be suitable for less demanding indoor conditions.
3. Type of Fastener
There are various fastener types, each suited for different applications:
- Bolts: Threaded fasteners that generally require nuts to join components.
- Screws: Designed with threads to be driven directly into materials like wood or metal.
- Nails: Non-threaded fasteners typically used to join items through friction.
- Nuts: Used with bolts to create a strong connection.
- Washers: Thin discs that disperse pressure and protect surfaces.
- Rivets: Permanently join materials from the front and back.
4. Material Selection
Choosing the right material is critical to performance. Common materials include steel, stainless steel, aluminum, brass, bronze, copper, and plastic. Each material has its advantages based on mechanical needs and environmental conditions.
5. Coating
Coatings can extend the life of fasteners by improving corrosion resistance. Popular coatings include zinc for moisture protection, galvanizing for rust resistance, and specialty coatings for industrial applications requiring additional protection.
6. Drive Type
Drive types determine how fasteners are installed. Common options include:
- Phillips Drive: A cross-shape for secure connections.
- Flathead (Slotted): For less torque applications.
- Torx (Star-shaped): Provides higher torque without slipping.
- Hex Drive: Frequently used with an Allen key or hex driver.
7. Size
Correct sizing ensures proper installation. Measure the thread size, pitch, and length to match the materials being joined. Proper head style and shape based on project needs ensure correct torque and accessibility.
8. Compatibility
Ensure compatibility between fasteners and the materials they connect. Corrosion-resistant fasteners should be used in harsh environments to improve durability. Using fasteners made from the same material as the structure prevents galvanic corrosion.
9. Industry Standards
Fasteners must meet industry standards such as ASTM, ISO, and ANSI for strength, dimensions, and materials. Compliance ensures reliability and safety in demanding applications.
10. Maintenance
Consider long-term maintenance. Will the fastener require regular tightening? Is it easily accessible? Planning ahead can save time and reduce future maintenance costs.
Frequently Asked Questions
How do I measure a fastener like a bolt or screw?
Fastener length is measured differently depending on the design. For fasteners with the head above the surface, the measurement is from under the head to the tip. For countersunk fasteners, measure from the head’s surface to the tip.
How do metric fasteners differ from imperial fasteners?
Imperial fasteners use threads per inch (TPI), while metric fasteners use thread pitch, which measures the distance between thread peaks in millimeters. It’s essential to use the correct system for compatibility.
What is the difference between threaded and non-threaded fasteners?
Threaded fasteners like screws and bolts have ridges and are used with nuts or tapped holes. Non-threaded fasteners like rivets create permanent connections.
What should I be careful about when measuring a fastener?
Use precision tools like calipers to measure length, thread size, and pitch. Ensuring the fastener meets specifications is crucial for proper fit and performance.